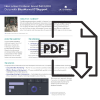
A midstream gas producer sought to improve its maintenance practices for critical infrastructure, focusing on valves and instrumentation at its export terminal. By leveraging BlueMarvel OT Support in collaboration with a BlueMarvel partner, the company identified and proactively addressed a recurring ice buildup issue on a 16-inch control valve. This resulted in zero valve magnet failures, a significant reduction in alerts, and the prevention of potential $500,000 daily production losses.
About the Customer
The customer operates a midstream export terminal that plays a crucial role in transporting propane to international markets. Given the harsh coastal environment, the company’s success relies on the reliable performance of its critical valves and instrumentation.
The Challenge
The export terminal faced two major challenges:
- Developing Better Maintenance Practices – The gas producer required an improved system to identify, track, and resolve valve and instrumentation issues efficiently.
- Accessing the Right Expertise – Once issues were identified, the company struggled to find specialized expertise quickly, leading to prolonged downtime.
Each valve failure jeopardized daily operations, posing a significant risk of revenue loss and operational disruptions.
The Solution
The gas producer’s BlueMarvel partner deployed the BlueMarvel OT Support app to address these challenges:
- Comprehensive Monitoring – Real-time data and alerts provided early detection of potential valve issues.
- Efficient Resource Deployment – The app enabled faster problem identification, allowing quick mobilization of the right resources.
- Knowledge Sharing & Collaboration – Centralized documentation ensured all stakeholders had access to critical operational insights, fostering consistency and efficiency.
This systematic approach allowed the partner to implement scalable and sustainable maintenance solutions tailored to the gas producer’s needs.
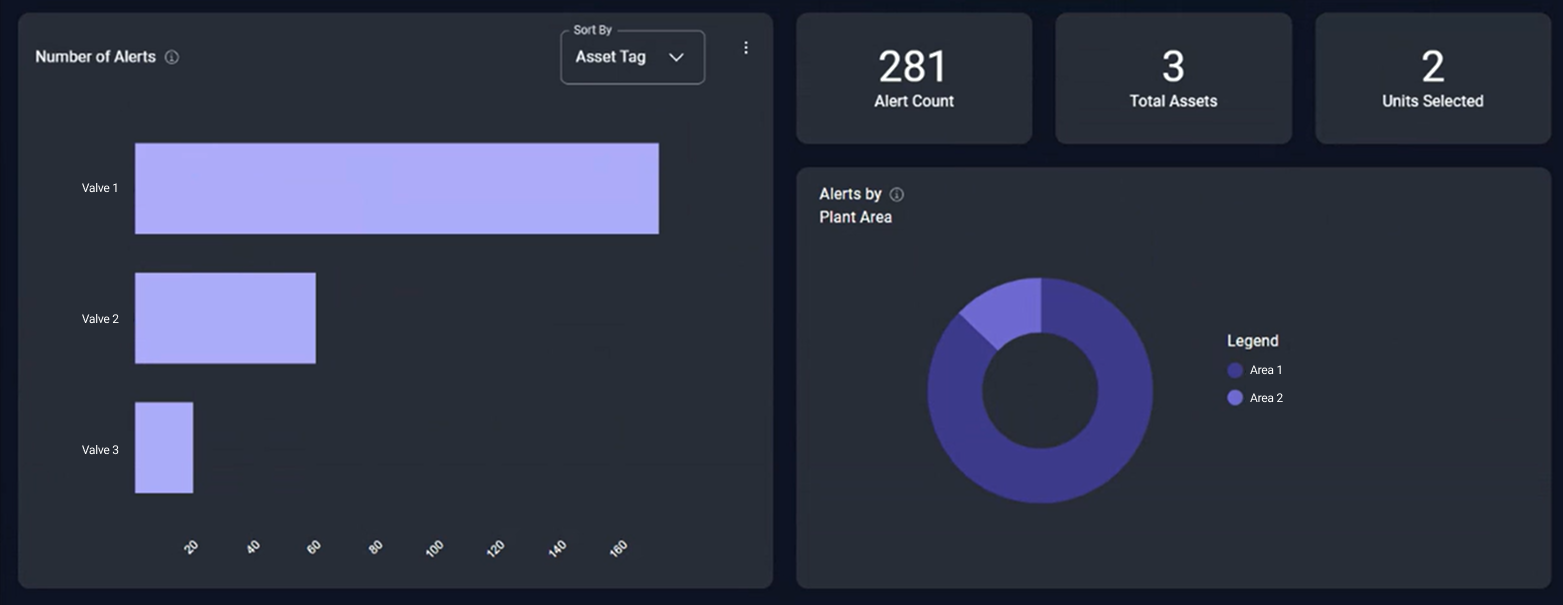
Implementation & Experience
The BlueMarvel partner introduced field-to-cloud data integration, enabling:
📡 Seamless Data Transfer - Real-time operational data streamed directly to the BlueMarvel cloud.
🤝 Collaborative Workflows - Improved communication between site teams, corporate HQ, and mobile users.
⚡ Streamlined Decision-Making - OT Support’s integrated expertise enhanced response times and preventative strategies. By fostering ongoing collaboration and knowledge continuity, BlueMarvel OT Support became an essential tool for operational efficiency.
The Outcome
In late October, the export terminal identified an ice buildup issue on its 16-inch control valve, leading to magnet degradation. A complete valve failure occurred within a month, highlighting the urgency for a proactive solution. With BlueMarvel OT Support, the gas producer and its partner took immediate action:
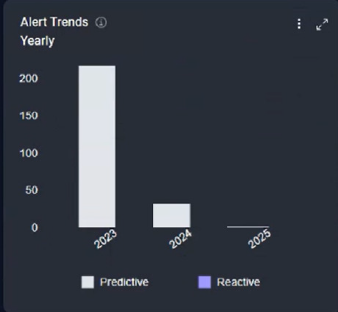
Early Warning Detection – Travel deviation and drive signal alerts pinpointed developing issues before failure. Device alerts went from over 200 to 50 YoY for the ice buildup issue.
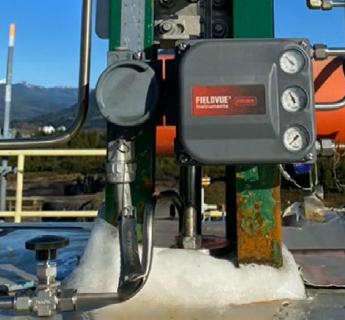
Proactive Maintenance Implementation – A dry air purge system was installed to prevent future ice buildup.
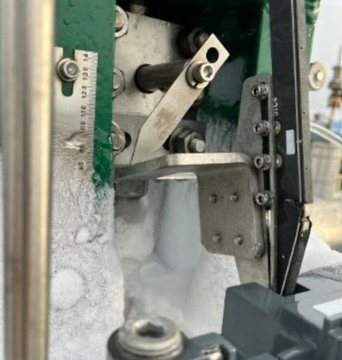
Zero Failures, Significant Cost Avoidance – Since implementing the solution, no further magnet failures have occurred, saving the company $500,000 in potential daily losses.
💬 “These tools are not just dashboards of alerts they’re transforming how we approach predictive maintenance and optimize our operations.”
Future Plans & Ongoing Success
Following this success, the gas producer expanded OT Support across five additional facilities. The company also integrated BlueMarvel applications - OperationsMetrics and ControlPerformance as part of a larger corporate-driven centralized monitoring initiative.
Future opportunities include:
🔍 Predictive Monitoring – Enhancing failure prevention strategies.
⚡ Energy Management – Optimizing operational efficiency.
🔗 Deeper Partner Collaboration – Strengthening the BlueMarvel partner relationship for continuous improvements.
Key Takeaways & Lessons Learned
🔹 Proactive monitoring prevents costly operational failures.
🔹 Documenting maintenance strategies ensures knowledge continuity.
🔹 Collaboration with solution providers enhances tool adoption and long-term value.
Want to see how BlueMarvel OT Support can enhance predictive maintenance and improve operational efficiency?
Contact us today to book a demo and explore the possibilities for your business. 🚀